The Curious Cat Management Blog Carnival has been published since 2006. The carnival, published twice a month, links to great, recent, management blog posts. I hope you find these post interesting and find some new blogs to start reading. Follow me online: Google+, Twitter and elsewhere.
- How to Build it: Lean Prototyping Techniques for Hardware – “Good user feedback is essential, and this feedback should guide making the next round of prototypes. It is an iterative cycle. The key to making good products is making mistakes early and learning from them. This is best done through prototyping and getting user feedback.”
- 3 Reasons Why Layoffs Don’t Benefit Hospitals in the Long Run by Bob Herman – “Dr. Gruner says ThedaCare has had a “no layoff” philosophy and commitment to Lean techniques, similar to Scripps, since 2003. He agrees with Mr. Van Gorder, saying layoffs are only a patchwork strategy with immediate financial gains and long-term financial and cultural losses. However, focusing on the retention of employees without layoffs is actually the simpler strategy — it just requires an undying commitment and focus.”
- The Greatest Waste by John Hunter – “The sentiment of failing to use the ability of people is not that uncommon. But putting the thought and effort behind changing that failure is. Dr. Deming consistently re-inforced the creation of a management system that sought to take advantage of the ability of people.”
- Coach Says: What Do You Think? by John Shook – “Your challenge will be to find a way to reconcile the apparent contradiction. You need to reconcile them not to satisfy the sensei (absolutely not for that reason) but to deepen your own learning. Presume that there is some truth in what both sensei are telling you. You need to determine just what that truth is and how you can make sense of it in this specific situation.”
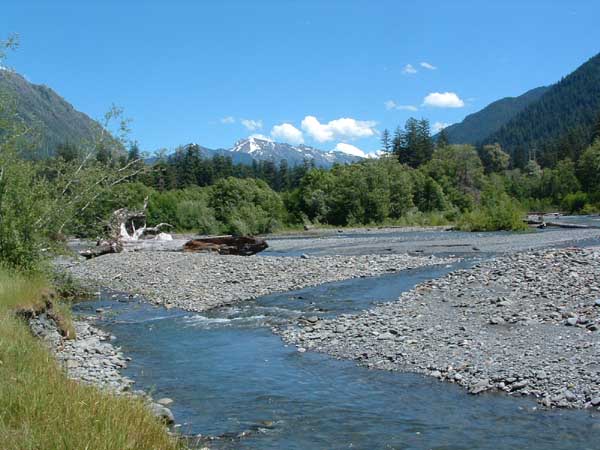
Hoh River Trail, Hoh River trail, Hoh Rainforest, Olympic National Park by John Hunter
Respect for Everyone
TL;DR – The two pillars of the Toyota Way are: respect for people and continuous improvement.
One of the big reasons my career followed the path it did (into management improvement) was due to the impact of respect for people. My father was a professor (in statistics, engineering and business) and consulted with organizations to help them achieve better results. To achieve results he took advantage of the gains possible when using statistical tools to manage with respect for people.
Managing Our Way to Economic Success: Two Untapped Resources, 1986: “American organizations could compete much better at home and abroad if they would learn to tap the potential information inherent in all processes and the creativity inherent in all employees.”
After he died, for years, people would talk to me about the difference he made in their lives (at conferences mainly). Other than those with PhD’s in statistics (of which there were many, but a very small number compared to all the others) the thing that made a difference was respect for people. Those who chose to talk to me are obviously a self selected group. But of those, the people that made the largest impact on me basically said he talked to me as though everything I said mattered. He didn’t talk down to me. He helped me see how I could help improve: the organization and my own skills and abilities.
This didn’t happen 5 times or 10 times of 20 times, it happened many more times than that. Year after year of this helped push me to stick with management improvement. These served as a great incentive to perserve as I ran into the typical difficulties actually improving management systems.
The senior executives he talked to were not very impressed that he spoke to them with respect. So none mentioned that with awe, but a few did notice that he was able to connect with everyone – the senior executives, nurses, people on the factory floor, secretaries, salespeople, front line staff, engineers, janitors, middle managers, doctors, union leaders. The senior executives were more likely to be impressed by the success and his technical ability and knowledge as well as communication skill. Doctors, statisticians and engineers were more impressed with knowledge, technical skill, skill as a teacher and advice.
Continue reading →