I believe net neutrality should be championed to prevent decay of the usability of the internet. It seems to me internet connectivity is a natural monopoly that economic theory says should be a regulated monopoly. Smart countries have invested in providing much better internet connectivity that the USA has at much lower prices. Now in the USA we have companies that seek to control internet connectivity and then use that monopolistic control to favor higher margin efforts. So force those that have resources available on the internet to pay or the ISP threatens to degrade the connectivity to their resources.
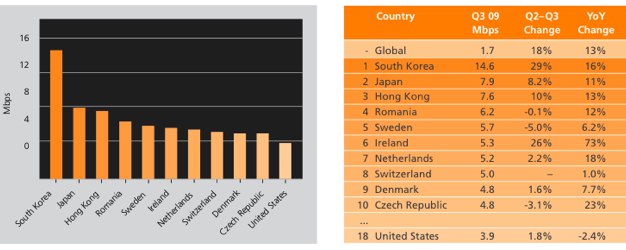
The investment in equipment and fiber that allows internet connectivity has to be paid for. If those regulated ISPs wanted to set bandwidth use pricing that is fine with me. If we decided it is best to have one low price say $30 a month for access at a similar perforance of 10 other countries (Japan, Germany, South Korea, Canada, United Kingdom…) and then charge extra for individuals those that use more than some amount fine. But I think it should not be tied to whether you use service that haven’t paid the ISP money to be favored. The USA is currently 18th and slowed down, while others continue to speed up.
The 2008 ITIF Broadband Rankings show the USA in 15th place, out of 30 OECD countries, for broadband adoption, speed and price. In 2001 the USA was in 4th place.
If ISPs don’t want to be in the business they should be in – providing internet connectivity. Fine, get out of that business and go into the business they want to be in. But don’t try to take control of a natural monopoly and then use that control to extort money from those that rely on the natural monopoly.
Google accused of YouTube ‘free ride’
Some of Europe’s leading telecoms groups are squaring up for a fight with Google over what they claim is the free ride enjoyed by the technology company’s YouTube video-sharing service. Telefónica, France Telecom and Deutsche Telekom all said Google should start paying them for carrying bandwidth-hungry content such as YouTube video over their networks.
I can understand why they would think that way. But isn’t it equally valid to say hey those that pay you for internet connectivity really want to use YouTube. If you need to make more investments in your infrastructure to support your customers use, then do so and raise the prices. I completely disagree with the ISP negotiating what content users can see. But if that were to happen why couldn’t Google instead of paying say, hey your customers really want YouTube – if you don’t pay us we won’t let you deliver it to your customers?
Net Neutrality: This is serious by Tim Berners-Lee
When I invented the Web, I didn’t have to ask anyone’s permission. Now, hundreds of millions of people are using it freely. I am worried that that is going end in the USA.
…
Yes, regulation to keep the Internet open is regulation. And mostly, the Internet thrives on lack of regulation. But some basic values have to be preserved. For example, the market system depends on the rule that you can’t photocopy money. Democracy depends on freedom of speech. Freedom of connection, with any application, to any party, is the fundamental social basis of the Internet, and, now, the society based on it.
Let’s see whether the United States is capable as acting according to its important values, or whether it is, as so many people are saying, run by the misguided short-term interested of large corporations.
I hope that Congress can protect net neutrality, so I can continue to innovate in the internet space. I want to see the explosion of innovations happening out there on the Web, so diverse and so exciting, continue unabated.
Google’s Traffic Is Giant, Which Is Why It Should be Your ISP
Continue reading →
Net Neutrality, Policy, Economics and Intelligent Engineering
I believe net neutrality should be championed to prevent decay of the usability of the internet. It seems to me internet connectivity is a natural monopoly that economic theory says should be a regulated monopoly. Smart countries have invested in providing much better internet connectivity that the USA has at much lower prices. Now in the USA we have companies that seek to control internet connectivity and then use that monopolistic control to favor higher margin efforts. So force those that have resources available on the internet to pay or the ISP threatens to degrade the connectivity to their resources.
The investment in equipment and fiber that allows internet connectivity has to be paid for. If those regulated ISPs wanted to set bandwidth use pricing that is fine with me. If we decided it is best to have one low price say $30 a month for access at a similar perforance of 10 other countries (Japan, Germany, South Korea, Canada, United Kingdom…) and then charge extra for individuals those that use more than some amount fine. But I think it should not be tied to whether you use service that haven’t paid the ISP money to be favored. The USA is currently 18th and slowed down, while others continue to speed up.
The 2008 ITIF Broadband Rankings show the USA in 15th place, out of 30 OECD countries, for broadband adoption, speed and price. In 2001 the USA was in 4th place.
If ISPs don’t want to be in the business they should be in – providing internet connectivity. Fine, get out of that business and go into the business they want to be in. But don’t try to take control of a natural monopoly and then use that control to extort money from those that rely on the natural monopoly.
Google accused of YouTube ‘free ride’
I can understand why they would think that way. But isn’t it equally valid to say hey those that pay you for internet connectivity really want to use YouTube. If you need to make more investments in your infrastructure to support your customers use, then do so and raise the prices. I completely disagree with the ISP negotiating what content users can see. But if that were to happen why couldn’t Google instead of paying say, hey your customers really want YouTube – if you don’t pay us we won’t let you deliver it to your customers?
Net Neutrality: This is serious by Tim Berners-Lee
…
Yes, regulation to keep the Internet open is regulation. And mostly, the Internet thrives on lack of regulation. But some basic values have to be preserved. For example, the market system depends on the rule that you can’t photocopy money. Democracy depends on freedom of speech. Freedom of connection, with any application, to any party, is the fundamental social basis of the Internet, and, now, the society based on it.
Let’s see whether the United States is capable as acting according to its important values, or whether it is, as so many people are saying, run by the misguided short-term interested of large corporations.
I hope that Congress can protect net neutrality, so I can continue to innovate in the internet space. I want to see the explosion of innovations happening out there on the Web, so diverse and so exciting, continue unabated.
Google’s Traffic Is Giant, Which Is Why It Should be Your ISP
Continue reading →