The Curious Cat Management Improvement Carnival has been published since 2006 and this is the 200th edition. The posts selected for the carnival focus on the areas of management improvement I have focused on in the Curious Cat Management Improvement Guide since 1996 (17 years now, which I find pretty amazing): Deming, lean thinking, leadership, innovation, respect for people, customer focus, etc..
- Eiji Toyoda – the Master Innovator by Bill Waddell – “He was a master innovator in the days when innovation wasn’t cool, and his focus was not so much on the product as it was on the processes – on management.”
- The Man Who Saved Kaizen by Jon Miller – “Eiji Toyoda led from the front. His message to leaders within Toyota: ‘I want you to use your own heads. And I want you actively to train your people on how to think for themselves.'”
- The consumer is the most important point on the production-line by John Hunter – “The continued view of the organization as a hierarchical pyramid of authority and responsibility hides the connection of the customer/user to the processes in our organizations.”
- Lean IT at Toyota by Pierre Masai – “educate yourself on the subject, since so many stories of dramatic or step-by-step improvements do exist out there. Then, soon after, experiment yourself. This is the basis of TPS. Make sure you also get enthusiastic people on board, and take the support of experienced external coaches if you need this to get started. Create a culture within your company where the principles of lean become embedded in everything you do.”
- What Looks Like A People Problem Is Often A Situation Problem by Bret Simmons – “It’s easier to blame and flame people than it is to fix the crappy systems that are often the root cause of unacceptable performance and behavior in our organizations.”
- Demotivating Employees One Performance Review At A Time by Gregg Stocker – “Effective leaders talk to those on their teams. They coach and develop on a continual basis, rather than wait for the once or twice per year performance review.”
- Fight for the facts by Wally Bock – “Sometimes opinions show up pretending to be facts. That’s when someone shares only the facts they think will support their opinion. Ask for sources. Search for facts that support another position… Facts are important. Fight for them.”
- The Term “Lean Production” is 25 Years Old – Some Thoughts on the Original John Krafcik Article by Mark Graban – “Lean is respect for humanity and continuous improvement… Lean is an integrated management and operational system…”
- Nearly 40 percent of the CEOs on the highest-paid lists from the past 20 years were eventually “bailed out, booted, or busted.” by Sarah Anderson, Scott Klinger and Sam Pizzigati – “The Bailed Out: CEOs whose firms either ceased to exist or received taxpayer bailouts after the 2008 financial crash held 22 percent of the slots in our sample. Richard Fuld of Lehman Brothers enjoyed one of Corporate America’s largest 25 paychecks for eight consecutive years — until his firm went belly up in 2008.
The Booted: Not counting those on the bailed out list, another 8 percent of our sample was made up of CEOs who wound up losing their jobs involuntarily. Despite their poor performance, the “booted” CEOs jumped out the escape hatch with golden parachutes valued at $48 million on average.
The Busted: CEOs who led corporations that ended up paying significant fraud-related fines or settlements comprised an additional 8 percent of the sample. One CEO had to pay a penalty out of his own pocket for stock option back-dating. The other companies shelled out payments that totaled over $100 million per firm.” - General principles when thinking about roles by Jason Yip – “Adjust the roles to fit the people – not adjust the people to fit the roles.”
- Agile Brings Flexibility to Software Development by Matt Wrye – “Lean thinking is about creating flexibility in the manufacturing process in order to deliver the value that customer wants at that time.
In agile, this is also true… If new requirements come up during development, no problem. Add that requirement to the back log on the kanban board. The next time it is time to pull a new requirement the product owner can prioritize the new story at the top or not.
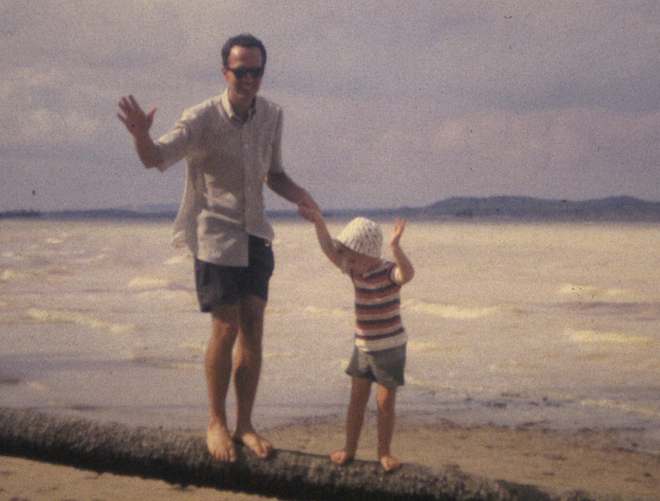
Dad, Bill Hunter and me in Malaysia.
Related: Curious Cat Management Improvement Carnival #1 – Curious Cat Management Improvement Carnival #100
Thank you for this summary – varied and interesting, something for everyone.
Pingback: Carnival of Quality Management Articles and Blogs – October 2013 | The world is too small? or Is it?